G’day, GN; wonder what that swine found so alluring about teh reporter’s trousers.
Mac --
Thanks for adding to your “origin story” late yesterday; sorry your pallet system didn’t catch on. 🙁
The kids got power back yesterday afternoon in Orlando; still lots of people without here in GA. May take until Sunday for some of them. Ditto for removal of downed trees.
We sure were lucky here at CasaK.
Maaaaaaaaan…I’m mighty foggy this morning for a guy who got seven hours of sleep. Buh.
Glad you missed the worst of it. I hope they get services back up soon. Hard to picture the vast size of the areas a hurricane hits. Texas tornadoes and even California earthquakes are more localized.
We really did luck-out; other areas of Gwinnett Cty. were not so fortunate. (Mostly downed power lines and trees; a few of the latter fell on houses.)
Erma certainly packed a lot of energy; it’s kind of sobering it engulfed pretty much the entire state of Florida. Friends in Jasper (NW GA) probably won’t have power back until sometime tomorrow; said they’ve got multiple downed power lines and trees in their area.
At least we had a few days to get ready…unlike a quake. But thanks to BetterHalfK’s efforts, we’re reasonably well-prepared re food, water and other stuff in the event of a significantly worse disaster with zero notice.
Sure Happy It’s Thursday, Gerbil Nation!
Good morning, Fatwa, and Mac!
I’ve always admired people who could make things with their hands. When I worked in defense electronics I worked with a German draftsman who was also a tool and die maker. He was the go-to guy for test fixtures of any type. I’d spend 10 or 15 minutes talking with him about what I needed and what it was supposed to do, give him a sample part, and he’d come up with an idea and whip up a dimensioned drawing in nothing flat. Of course he wasn’t allowed to build anything -- union rules -- I had to take the drawings down to the machine shop for that.
Paddy, when I had my shop I did a lot of that for Sandisk and others, though I made what I designed. It was really fun. I once designed and made a specimen holder for an electron microscope for National Semiconductor.
Sometimes I would be called in to design some modification for a machine. I would have to take measurements off the machine and figure out how I would mount things to it, then go back to the shop and design and build the tool or accessory. It was always tense until I knew it would fit and work.
Most time they would just describe what they needed to do and give me sample parts as you describe. I would design and build it. These were fun as I could design the tools to be built with my equipment and methods.
I also would make prototypes for parts that would be mass produced or molded. A mold would spit out very cheap parts but could cost 60 t0 80 grand to make so they paid me hundreds of dollars to make four or six they could test. These were challenging as molding uses different processes from machining and the tolerances were usually within one thousandth. Was fun.
At two of the CNC shops I worked at I was the only manual machinist and much of my work was designing and making fixtures or gauges for the CNCs like that. I had a lot of freedom and got along well with everyone. More fun.
They had this small board that plugged into the large board. There were so many wires they had trouble pulling them apart without damaging the board or bending the wires. They wanted something that would lift it straight up. I asked them if they wanted a bench or hand tool and they said either but a hand tool would be better. This is what I came up with.
It slipped between the boards and lifted straight up hitting the large board frame and the small board on a safe place. One arm is half length some of the boards had a lug in the middle.
It was easy to use and the employees liked it so much the first batch all disappeared into peoples drawers or kits so they knew where to find them. They ordered more tools several times, including a left hand version. When I took the first prototype in the department managers were walking around working the trigger like a figgitspinner, showing it off to others. This was a first model. I made the handles round, without the flats on the side, and with the stainless shank longer as they wanted to be sure they made contact for their anti-static straps. I liked this one. It was all 303 stainless steel and delron.
Another one. These connectors needed to be put on the boards so the fingers would be on the contact points to be soldered. They were pairs of fingers that touched each other. It was very hard to slip the board between the fingers and locate it correctly. I made this tool. The connector went on the front and the board went on the slide, located by the two tooling holes at the front. When the plunger was pushed it put the two together and they could be lifted off and sent to soldering. There were two feet at the back to hook on the edge of the table or bench so it could be worked with one hand. The slide was spring loaded.
They had test board like these with six or eight sockets. To release the test chip you pressed down on the spring loaded clamps on each side of the socket at the same time. They wanted something to hold all of the sockets open while they changed them with a vacuum wand. I made this. It has a delron base machined to support the board but clear all the stuff on the bottom. The lid presses all the release levers and latches down. I made a smaller one for the six socket board. All aluminum and delron except the catch which was stainless steel.
G’day, GN; wonder what that swine found so alluring about teh reporter’s trousers.
Mac --
Thanks for adding to your “origin story” late yesterday; sorry your pallet system didn’t catch on. 🙁
The kids got power back yesterday afternoon in Orlando; still lots of people without here in GA. May take until Sunday for some of them. Ditto for removal of downed trees.
We sure were lucky here at CasaK.
Maaaaaaaaan…I’m mighty foggy this morning for a guy who got seven hours of sleep. Buh.
Glad you missed the worst of it. I hope they get services back up soon. Hard to picture the vast size of the areas a hurricane hits. Texas tornadoes and even California earthquakes are more localized.
Hai, Mac!
We really did luck-out; other areas of Gwinnett Cty. were not so fortunate. (Mostly downed power lines and trees; a few of the latter fell on houses.)
Erma certainly packed a lot of energy; it’s kind of sobering it engulfed pretty much the entire state of Florida. Friends in Jasper (NW GA) probably won’t have power back until sometime tomorrow; said they’ve got multiple downed power lines and trees in their area.
At least we had a few days to get ready…unlike a quake. But thanks to BetterHalfK’s efforts, we’re reasonably well-prepared re food, water and other stuff in the event of a significantly worse disaster with zero notice.
Sure Happy It’s Thursday, Gerbil Nation!
Good morning, Fatwa, and Mac!
I’ve always admired people who could make things with their hands. When I worked in defense electronics I worked with a German draftsman who was also a tool and die maker. He was the go-to guy for test fixtures of any type. I’d spend 10 or 15 minutes talking with him about what I needed and what it was supposed to do, give him a sample part, and he’d come up with an idea and whip up a dimensioned drawing in nothing flat. Of course he wasn’t allowed to build anything -- union rules -- I had to take the drawings down to the machine shop for that.
Paddy, when I had my shop I did a lot of that for Sandisk and others, though I made what I designed. It was really fun. I once designed and made a specimen holder for an electron microscope for National Semiconductor.
Sometimes I would be called in to design some modification for a machine. I would have to take measurements off the machine and figure out how I would mount things to it, then go back to the shop and design and build the tool or accessory. It was always tense until I knew it would fit and work.
Most time they would just describe what they needed to do and give me sample parts as you describe. I would design and build it. These were fun as I could design the tools to be built with my equipment and methods.
I also would make prototypes for parts that would be mass produced or molded. A mold would spit out very cheap parts but could cost 60 t0 80 grand to make so they paid me hundreds of dollars to make four or six they could test. These were challenging as molding uses different processes from machining and the tolerances were usually within one thousandth. Was fun.
At two of the CNC shops I worked at I was the only manual machinist and much of my work was designing and making fixtures or gauges for the CNCs like that. I had a lot of freedom and got along well with everyone. More fun.
It’s dangerous to get Mac talking about machining.
Hai, Paddy!
Oh noes…enthusiasm!! Aaaaaaaaaaah…
Exclamation points!!!!!!
One of the problems Sandisk had.
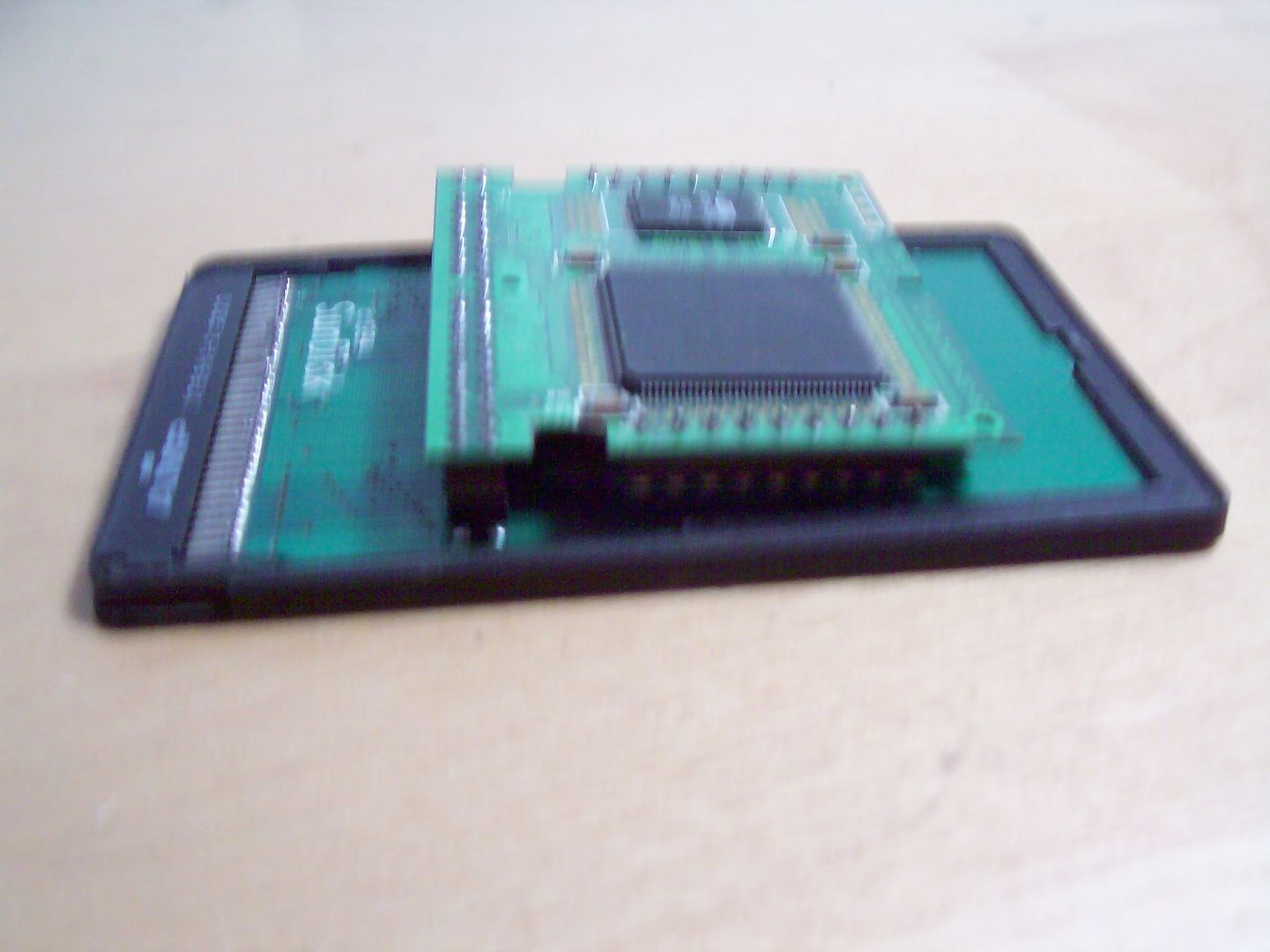
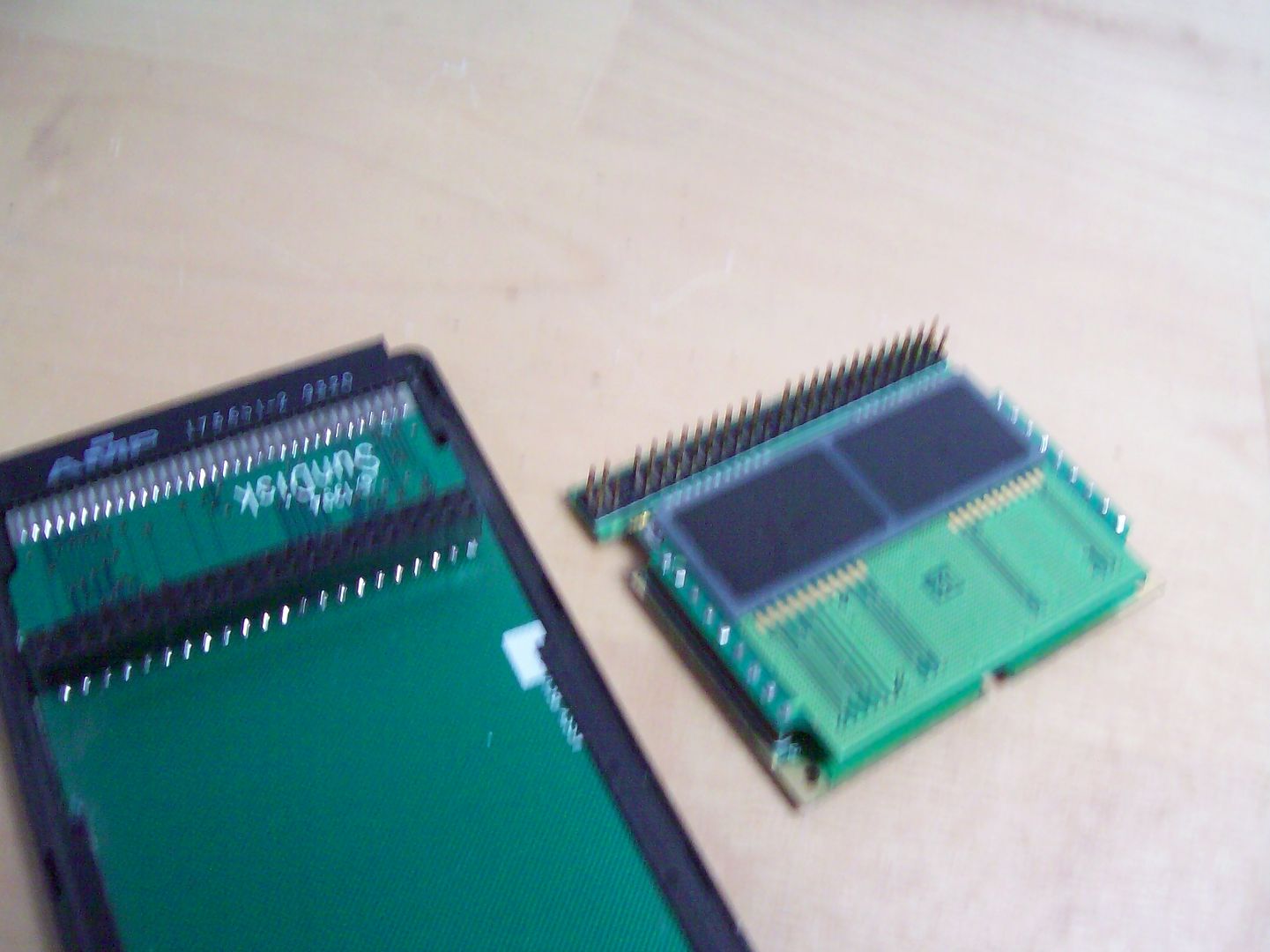
They had this small board that plugged into the large board. There were so many wires they had trouble pulling them apart without damaging the board or bending the wires. They wanted something that would lift it straight up. I asked them if they wanted a bench or hand tool and they said either but a hand tool would be better. This is what I came up with.
It slipped between the boards and lifted straight up hitting the large board frame and the small board on a safe place. One arm is half length some of the boards had a lug in the middle.
It was easy to use and the employees liked it so much the first batch all disappeared into peoples drawers or kits so they knew where to find them. They ordered more tools several times, including a left hand version. When I took the first prototype in the department managers were walking around working the trigger like a figgitspinner, showing it off to others. This was a first model. I made the handles round, without the flats on the side, and with the stainless shank longer as they wanted to be sure they made contact for their anti-static straps. I liked this one. It was all 303 stainless steel and delron.
Another one. These connectors needed to be put on the boards so the fingers would be on the contact points to be soldered. They were pairs of fingers that touched each other. It was very hard to slip the board between the fingers and locate it correctly. I made this tool. The connector went on the front and the board went on the slide, located by the two tooling holes at the front. When the plunger was pushed it put the two together and they could be lifted off and sent to soldering. There were two feet at the back to hook on the edge of the table or bench so it could be worked with one hand. The slide was spring loaded.
They had test board like these with six or eight sockets. To release the test chip you pressed down on the spring loaded clamps on each side of the socket at the same time. They wanted something to hold all of the sockets open while they changed them with a vacuum wand. I made this. It has a delron base machined to support the board but clear all the stuff on the bottom. The lid presses all the release levers and latches down. I made a smaller one for the six socket board. All aluminum and delron except the catch which was stainless steel.